Smrštění, zvlnění a čas
InnovMetric a ShapeGrabber pomáhají společnosti MPC Molder provádět včasná rozhodnutí o výrobě autodílů.
S tím, jak se primární výrobky společnosti Miniature Precision Components (MPC) (tj. PCV ventily, konektory, hadičky, kování, zásobníky kapalin, plnicí uzávěry atd.) staly komoditními položkami s klesajícími ziskovými maržemi, začala společnost MPC nabízet výrobcům automobilů nové výrobky, mezi které patří kryty motorů s logy. Na rozdíl od téměř většiny předchozích výstupních komodit MPC se jedná o vysoce stylové díly: klenuté, embosované nebo rýhované. Výrobci automobilů je nazývají „pohledovými“ díly, jelikož jde právě o ty díly, které si v showroomech prodejců prohlížejí kupující.
Vzhledem k tomu, že tyto díly jsou několikanásobně větší než téměř cokoli, co společnost MPC dříve vyráběla, novými a obtížnými výzvami z hlediska zajištění kvality se stalo smršťování a zvlnění. Aby bylo možné zahájit výrobu podle plánu, byli technici nuceni udělat důležitá rozhodnutí o nástrojích a postupech v příliš krátké době a s příliš malým množstvím dat.
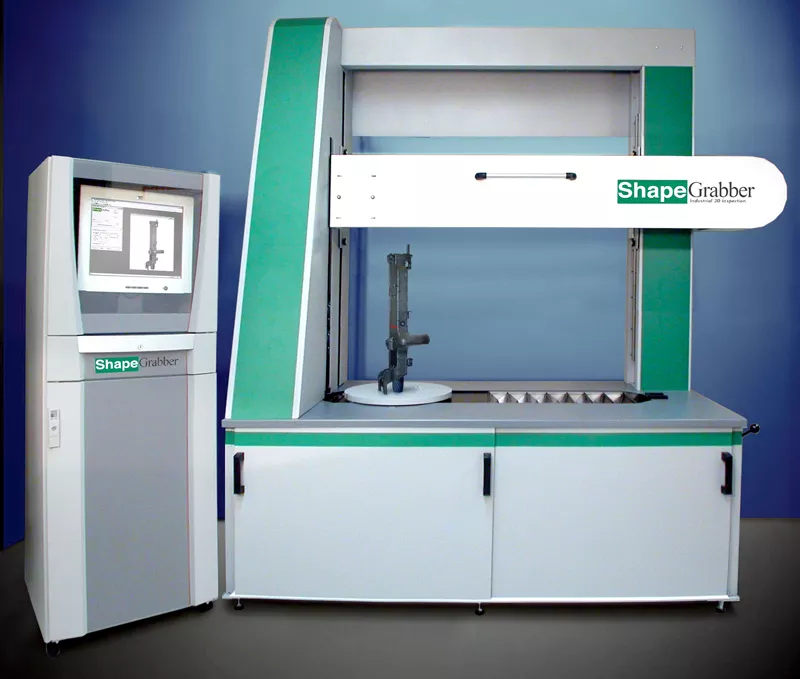
Samotné smrštění a zkroucení může snadno využít celou rozměrovou toleranci. Nevyhnutelné variace procesu vstřikování a lisování způsobují, že se díly posouvají ještě více mimo specifikace. Jako to u výrobců automobilů vždy bývá, čas je základní komoditou obchodních vztahů. Společnost MPC si může dovolit zahájit výrobu a odeslat vzorky dílů pouhé čtyři týdny od obdržení formy.
Rozměry se musí pohybovat v rámci tolerančního pásma (+/- 5 mm), aby vyhovovaly všem procesům, materiálům a variacím nástrojů.
Smrštění a zkroucení se řeší prostřednictvím:
- Změn procesu vstřikování
- Povolování tolerancí dílu
- Vybudování přípravku na chlazení
- Úpravy formy, která tvaruje díl
Výběr a implementace kteréhokoli z těchto postupů může snadno zabrat i čtyři týdny a následně nezbývá čas na odstraňování dalších problémů. „Čtyři týdny jsou jediné časové okno, kdy musíme vyladit a stabilizovat proces vstřikování,“ uvedl Clark a dodal „musíme vyřešit mnohem víc než jen smrštění a zvlnění.“
Společnost MPC vyřešila své problémy se smršťováním a zvlněním pomocí 3D laserového skeneru ShapeGrabber a inspekčního softwaru na bázi mračen bodů PolyWorks® od společnosti InnovMetric. Důvtipný management společnosti MPC proměnil řešení do dvou konkurenčních výhod: rychlejší uvedení na trh a vyšší stupeň zajištění kvality!
Výzva
Velkým problémem, s nímž se výrobci forem při smršťování a zvlnění potýkají, jsou různé příčiny těchto jevů. Smršťování je podmíněno materiálem; pohybuje se od 2 % do 14 % a může se lišit napříč šaržemi vstupního materiálu. Zvlnění souvisí s chlazením a návrhem použití tlustých a tenkých částí. Úspěšné řešení těchto rozměrových a tolerančních výzev vyžaduje mnoho analýz a výpočtů plus roky zkušeností.
Výrobci forem začínají navrhovat nový nástroj s odhadovanými hodnotami smrštění z bezpečnostního listu materiálu (MSDS) plastových peletek. Aby se výrobci forem mohli vypořádat se zkroucením, aplikují své znalosti o vtoku, ventilačních otvorech a umístění chladících cest. Dokud však není nástroj sestaven a spuštěn, jsou smršťování a zkroucení pouze kvalifikovanými odhady.
Nepostačující dotykové snímání, analýza toku ve formě a fotogrammetrie
Než přišlo laserové skenování a kontrola na bázi mračen bodů, neměli výrobci forem žádné nástroje pro kontrolu povrchu, které by byly komplexní a rychlé. Nejlepšími dostupnými metodami byly dotykové snímání pomocí souřadnicového měřicího stroje (CMM), analýza toku ve formě a fotogrammetrie. Všechny tyto metody však byly na některé věci příliš krátké.
Dotykové snímání
Dotykové snímání není schopno zachytit drobné hrbolky a poklesy a jak zdůrazňuje Clark, ani „jemnější jevy, jako například posun zvlnění v rozteči dvojice bodů X a Y, který zkroutí další bod mimo jeho toleranci Z“. To je důvod, proč důkladná kontrola povrchů vyžaduje 500 000 trojrozměrných (3D) bodů a někdy i milion nebo více místo třeba několika stovek, které poskytuje dotykové snímání.
Clark navíc dodává: „CMM trvá sedm pracovních dní, než se nastaví úloha, další dva dny zabere měření a dalších pět dní poté se shromáždí všechna data. Vzhledem k tomu, že CMM je neustále vytížen, možná budeme na své místo ve frontě muset čekat dalších sedm dní. Takže při metodě „bod po bodu“ máme v nejlepším případě jen dva pokusy, abychom vše udělali správně.“
Analýza toku ve formě
Analýza toku ve formě je počítačová simulace, která předpovídá, jak se vstřikovaný plast bude smršťovat a kroutit na základě umístění a velikosti vtoků formy. Existují tři velké nevýhody:
- Používají se spíše nominální rozměry než data ze skutečné kontroly dílu; následné revize forem nelze snadno adaptovat.
- Předpovědi zvlnění jsou pouze teoretické a digitální. Abyste se u toku ve formě posunuli za virtuální říši, vyžaduje to vylepšení, která mohou výrobci forem odmítnout poskytnout.
- Jako každá simulace, i analýza toku ve formě obsahuje implicitní předpoklady a číselné hodnoty, které nemusí v reálném světě obstát.
„Potřebujeme vědět, k čemu ve formě skutečně došlo, ne co se mělo stát,“ řekl Clark. Analýza toku ve formě je také nákladná (stojí až 12 000 USD na nástroj) a obvykle zabere dva z vyhrazených čtyř týdnů.
Fotogrammetrie
Fotogrammetrie je doslova měření pomocí fotografie ve vysokém rozlišení. Fotogrammetrie zachycuje povrchy několikrát větší než laserové skenery, ale pro zarovnání mohou být nutné nalepené značky. Jakmile jsou fotografie digitalizovány, lze je snadno porovnat se staženým CAD souborem nebo je lze nahrát do CAD souboru jako záplatu povrchu.
Fotogrammetrie byla odzkoušena jako alternativa ke kontrole přípravků a měřidel svazků podtlakových trubek motoru. „Problém kontroly spočívá v tom, že pro každý motor je nutná jiná,“ řekl Clark. „Za 13 let, co jsem tady, jsme zakoupili přes tisíc měřidel, která pravděpodobně stála celkem 3,5 milionu dolarů. Jde o černé díly, takže se špatně fotí, pokud je to vůbec možné,“ dodal. „Vždy máme přitom problém s okolním světlem a vnímáním hloubky v ose Z.“
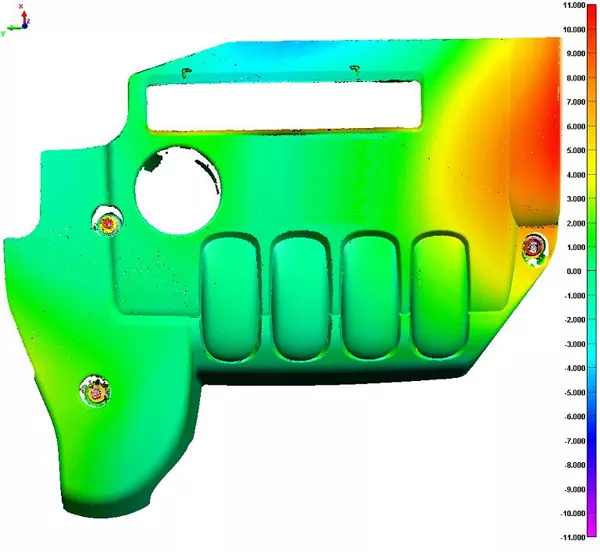
Barevná mapa porovnání dat a CAD
Řešení
Pro kontrolu plastových dílů používá společnost MPC skener ShapeGrabber Ai810C. Tento víceosý 3D skener umožňuje uživateli požádat o kompletní naskenování dílů jediným kliknutím myši, o zbytek se postará systém.
Toto snadné použití je výsledkem používání více os skenování (horizontální a vertikální), stejně jako třetí rotační osy, na kterou je díl umístěn. Všechny tyto osy jsou kalibrovány do stejného referenčního snímku, takže se automaticky zarovná více skenů. Nastavením požadovaných skenů pro daný díl předem lze kompletní sadu skenů snadno automatizovat.
Proces nastavení zabere jen několik minut díky velmi velké hloubce ostrosti (DOF) skenovacích hlav. Tato velká DOF umožňuje nastavit skeny pomocí jednoduchého a intuitivního grafického uživatelského rozhraní, protože není nutné přesně sledovat složitý obrys dílu jako u většiny ostatních skenerů.
Skenovací hlavy získávají data rychlostí od 18 000 do 150 000 bodů/s. Vygenerování úplného mračna bodů představujícího díl tedy zabere pouze několik minut. Tento datový soubor je následně pro dokončení procesu kontroly snadno zpracován programem PolyWorks|Inspector™.
Kombinace rychlosti a snadného použití skeneru zpřístupňuje skener většímu počtu uživatelů a zkracuje dobu nastavování a kontroly, což výrazně snižuje náklady na kontrolu ve srovnání s alternativními metodami.
Data, které společnost MPC potřebuje, jsou k dispozici za 15 minut, nikoliv za několik dnů
Kontrola na bázi mračen bodů v PolyWorks
Kontroly krytu motoru společnosti MPC se nyní provádějí pomocí barevných map tolerancí v modulu PolyWorks|Inspector. PolyWorks porovnává miliony datových bodů získaných skenerem s referenčním CAD modelem. Experti ze společnosti MPC nastaví v PolyWorks tolerance, aby určili přijatelné a nepřijatelné odchylky mezi datovými body a CAD modelem. Zobrazení využívá celé barevné spektrum od červené (plusové tolerance, příliš mnoho materiálu) až po modrou (mínusové tolerance, příliš málo materiálu). Jelikož je toleranční pásmo barevné mapy nastavitelné, jde o vynikající nástroj pro analýzy typu „co-kdyby“. „Barevné mapy nám umožňují vidět, co se skutečně děje uvnitř formy, které povrchy jsou ovlivněny změnou tolerance a jak moc,“ vysvětluje Clark. „To, co nám barevná mapa skutečně ukazuje,“dodal, „je to, jak plastový díl plave uvnitř formy. Víme, že materiál dílu se smršťuje do správných rozměrů a zkroucení během ochlazování jej přivede do tvaru, který si přál designér.“
Pokud inženýři společnosti MPC potřebují zkontrolovat něco, co nebylo původně specifikováno v rozvržení kontroly, stačí, když kliknou na bod v datech nebo přidají body opětovným naskenováním. V každém případě jde o záležitost několika minut. V minulosti bylo nutné přeprogramovat CMM. „Abyste mohli přidat, byť jen jeden bod u dotykové sondy, museli jste začít od znovu,“ řekl Clark. „A nikdy to nebylo hotovo za méně než dva dny.“
Pro uživatele ve společnosti MPC a její zákazníky byly ShapeGrabber a PolyWorks jediným systémem, který dokázal:
- Držet krok s rychlostí výroby a četností kontrol.
- Projít standardními testy opakovatelnosti a reprodukovatelnosti (R&R), kterými se certifikují kontrolní systémy.
V testu R&R operátor třikrát změří prvek na 10 dílech. Následně druhý operátor změří stejnou vlastnost na stejných 10 dílech ještě třikrát a výsledky se porovnají. Systémy PolyWorks a ShapeGrabber těmito testy úspěšně prošly.
Všechny ostatní přístupy na bázi laseru byly poněkud pomalé. Žádný z nich nedokázal shromáždit potřebná data za méně než dvě nebo tři hodiny.
„Během několika minut, namísto dvou nebo tří týdnů, nám skenování dokáže dodat veškerá data povrchů, která potřebujeme, abychom si mohli vybrat z možností výroby,“ řekl Clark. „Zarovnání a formátování z PolyWorks získáváme velmi blízko reálného času. Ale hlavně, máme dostatek času, abychom mohli udělat těžká výrobní rozhodnutí.“ A záhy dodal: „Vzhledem k tomu, že dokážeme shromáždit veškerá potřebná data o rozměrech a tolerancích tak rychle, máme několik dalších dní na inženýrství a analýzu každé zakázky. Tento čas navíc je obrovskou pomocí, když se rozhodujeme, zda hledat volnější tolerance, upravit nástroj, nějakým způsobem upravit proces nebo nechat vyrobit chladicí přípravek.“
Ušetřený čas také znamená, že se technici mohou vrátit a podívat se na věci novým pohledem. To může zahrnovat podezřelé oblasti v nové dávce vzorových dílů. „ShapeGrabber a PolyWorks nám pomáhají během celého procesu nastavení,“ poznamenal Clark.
„Věříme, že společnost MPC dosáhla se systémem ShapeGrabber a PolyWorks návratnost investic (R-O-I) do dvou týdnů,“dodal. „Poskytli nám dvě nové výhody oproti konkurenci: nekompromisní zajištění kvality a rychlé zahájení výroby. Díky 3D skenování a kontrole na bázi mračen bodů nyní máme několik dalších dní na to, abychom učinili zásadní obchodní rozhodnutí. ShapeGrabber a InnovMetric nám pomohly během celého procesu nastavení,“vysvětlil Gregory Clark.
Výhody
Úspěch na náročném novém trhu
Skutečným testem účinnosti nové technologie je, zda její výhody přesahují potřeby uživatelů při jejich každodenních úkolech. Ve větších podnicích se tyto výhody projeví rychlejším zahájením výroby, delší dobou pro fáze inženýrství a analýz a větší flexibilitou metod.
Toto řešení nabídlo:
- Vylepšené zajišťování kvality, které pomáhá společnosti MPC zajistit, aby díly byly vstříknuty a vylisovány tak, jak je zapotřebí, tj. předtím, než jsou vzorky odeslány zákazníkům.
- Eliminování četných dodatečných rozměrových kontrol, což umožňuje dřívější zablokování nástrojů a procesů pro výrobu.
- Větší flexibilitu kontroly, která umožňuje vyhodnocení více výrobních možností a poskytuje více času na design formy a jeho odzkoušení. To se přímo promítá do nové konkurenční výhody společnosti MPC: lepší díly, dřívější dodání a spokojenější zákazníci.
- Kratší dobu uvedení na trh; společnost MPC nasbírá půl milionu až milion bodů z povrchu během několika minut, zatímco konkurenti plýtvají dny nebo týdny kontrolami pomocí dotykových sond.
- Lepší schopnost proniknout na nové trhy. Společnost MPC se jedním skokem přesunula od striktně funkčních, málokdy viděných dílů k vysoce stylovým krytům motoru, které má kupující na očích.
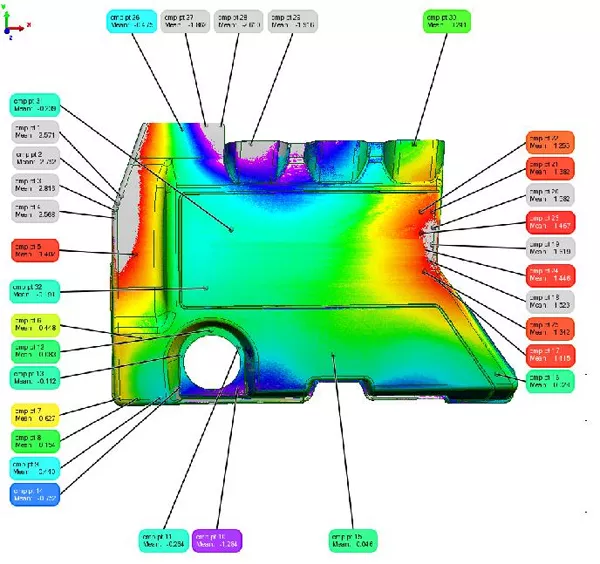