Ispezioni più veloci nella prototipazione rapida
O’Fallon Casting velocizza i processi di ispezione nella prototipazione rapida grazie a PolyWorks®.
Fondata nel 1969, O'Fallon Casting si dedica alla microfusione a cera persa di metalli non ferrosi nel suo stabilimento 20 minuti a ovest di St. Louis, MO. L’azienda fornisce getti ricavati da fusione per la prototipazione rapida e per la produzione in una vasta gamma di leghe di alluminio, leghe di rame e leghe composite con matrice di carburo di silicio. Dal 2006, O’Fallon Casting usa la scansione 3D e le soluzioni software PolyWorks® per effettuare ispezioni basate su nuvole di punti dei propri pattern e dei propri getti di fusione.
O’Fallon Casting di St. Louis, Missouri, è un'azienda leader nella microfusione a cera persa di metalli non ferrosi che ha costruito la sua reputazione producendo getti di alta qualità a prezzi competitivi per rispondere alle rigorose esigenze applicative degli utenti finali. Con il suo stabilimento di 4645 metri quadrati, l'azienda è specializzata nella produzione di getti a partire da una vasta gamma di leghe di alluminio, leghe di rame e leghe composite con matrice di carburo di silicio, e fornisce ai propri clienti il grezzo di fusione oppure il pezzo finito lavorato a macchina secondo quanto definito dalle specifiche del committente.
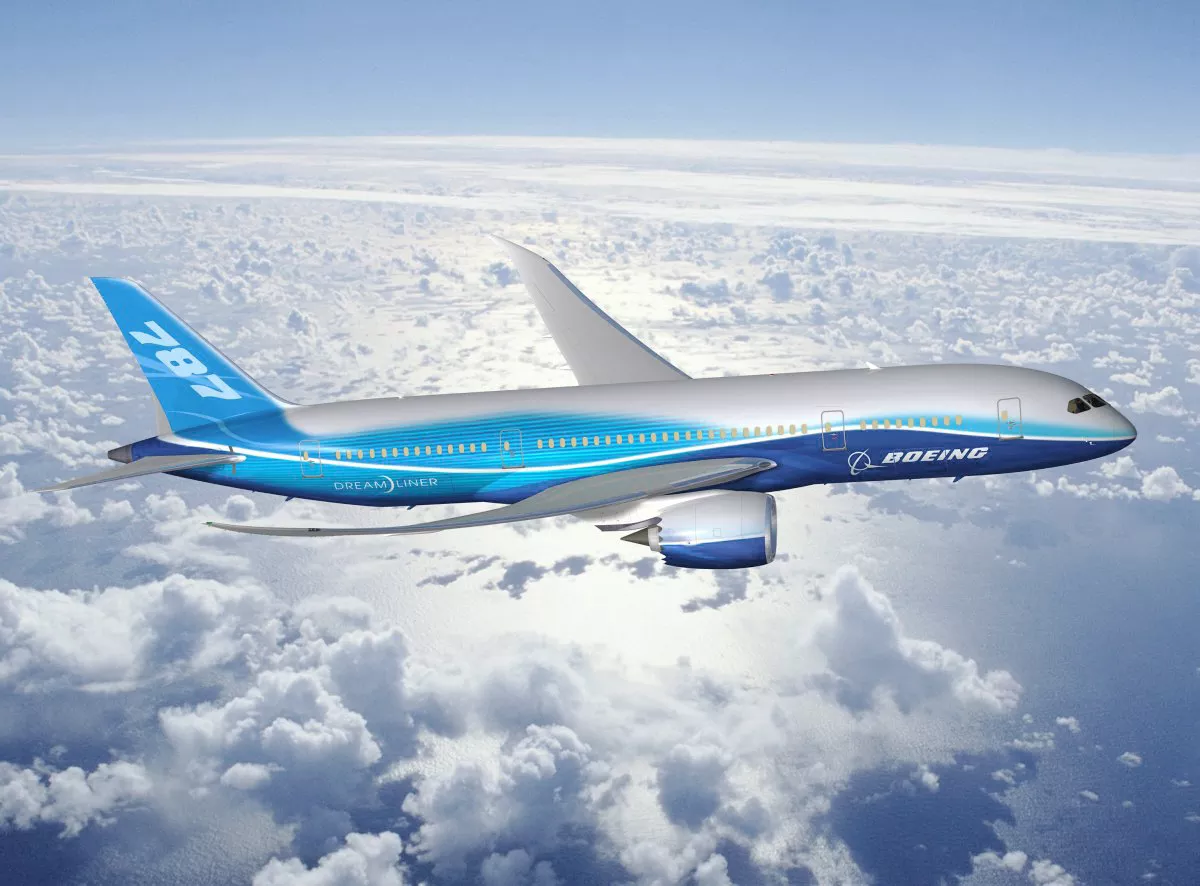
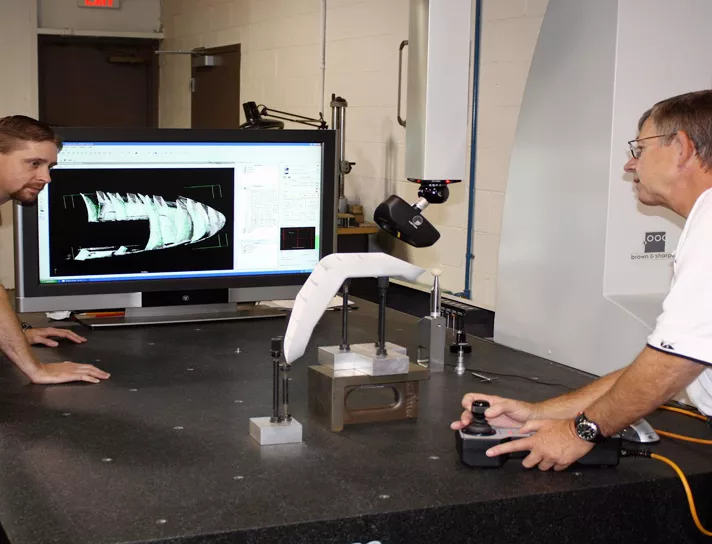
Ispezione del particolare con Ben Galmiche (a sinistra) e Ted Schnarre (a destra) di O’Fallon Casting Inc. con una CMM Global, uno scanner laser Metris XC50 e il software PolyWorks.
La sfida
O’Fallon Casting opera in una vasta gamma di mercati, oltre a quello della difesa (missilistica), quali: imballaggi per elettronica, valvole e pompe, apparecchiature medicali e dentali, macchinari di precisione automatici ad alta velocità, hardware, macchinari aziendali, robotica, apparecchiature ottiche e laser, apparecchiature di processo per wafer di silicio e per la produzione di semiconduttori.
Una delle aree di crescita dell’azienda è costituita dalla prototipazione rapida. Vengono utilizzati pattern generati a partire da un modello 3D contenuto in un file CAD per produrre un particolare velocemente e ottimizzando i costi, e verificare la bontà della progettazione prima della costruzione del modello da destinare alla produzione.
«Negli ultimi anni ci sono stati molti miglioramenti nella qualità delle finiture superficiali dei modelli, nella precisione e nelle opzioni di materiale; oggi i modelli sono più vicini alle near net shape offerte dal processo di microfusione a cera persa», spiega Ben Galmiche, ingegnere addetto alla qualità di O’Fallon Casting. Grazie a questi miglioramenti, la prototipazione rapida dei getti rappresenta un valore determinante per i clienti che intendono ridurre i costi generali legati alla lavorazione e lanciare rapidamente i prodotti sul mercato.
L’ispezione di qualità è un aspetto cruciale nell’industria della fonderia, e i metodi tradizionali di ispezione a contatto non si rivelavano adatti alla prototipazione rapida.
«In passato non avevamo metodi efficaci ed efficienti per ispezionare i modelli solidi. Avevamo una vecchia macchina di misura a coordinate di tipo a sbalzo, e usavamo una sonda a contatto per acquisire i dati dimensionali. Il processo era lento e stavamo cercando un’alternativa», spiega Galmiche.
La soluzione
Per migliorare i tempi di elaborazione del processo di ispezione dei prototipi rapidi, O’Fallon Casting ha scelto la scansione 3D e l’ispezione basata su nuvole di punti. O’Fallon Casting ha sostituito la precedente CMM con una Global della Hexagon Metrology accoppiata con un Metris XC50 Cross Scanner, uno scanner laser 3D multi-fascio ad alta velocità, progettato per l’ispezione delle entità geometriche dei particolari, che offre una distribuzione ottimale dei punti in tutte le direzioni. Questo nuovo sistema di misurazione 3D è stato fornito con la piattaforma software di metrologia 3D universale PolyWorks.
L’investimento ha dato prova di essere una di quelle spese che si ammortano rapidamente, in particolare quando O’Fallon Casting ricevette nel 2008 una richiesta di ispezione dell’alloggiamento di una delle luci poste alle estremità alari di un Boeing 787 Dreamliner.
Ecco come O’Fallon ha integrato in modo vincente l’analisi basata su nuvole di punti in tutte le fasi del processo di prototipazione rapida:
- È stato creato un modello dell’alloggiamento della luce all’estremità dell’ala a partire dal modello CAD 3D fornito dal cliente usando la SLA (stereolitografia) e la SLS (sinterizzazione laser selettiva).
- Quindi, il modello è stato ispezionato visivamente e manualmente per stabilire se fosse conforme al modello CAD di riferimento del particolare e se fosse stato adeguatamente proporzionato tenendo conto del ritiro.
- Una volta controllato e approvato il modello con il processo di ispezione di PolyWorks, O’Fallon Casting ha creato uno strato di ceramica intorno al pattern del prototipo.
- Il pattern con lo strato di ceramica è stato in seguito sottoposto ad un processo di tipo burn-out per vaporizzare il modello stesso, e lasciare il solo stampo in ceramica. La parte è stata colata da una fusione di alluminio A356, invecchiato artificialmente con il trattamento T6.
- Il particolare è stato quindi misurato attraverso una CMM Global ed uno scanner laser Metris XC50. I dati della nuvola di punti raccolti con questa procedura sono stati trasferiti elettronicamente a PolyWorks tramite la rete interna dell’azienda.
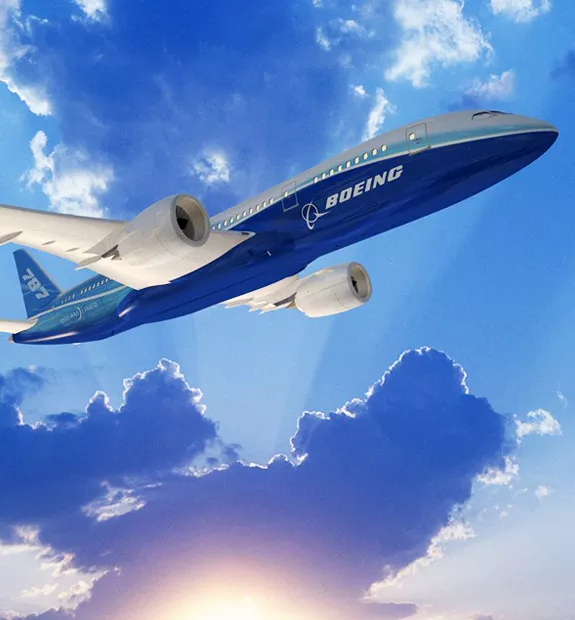
©Boeing
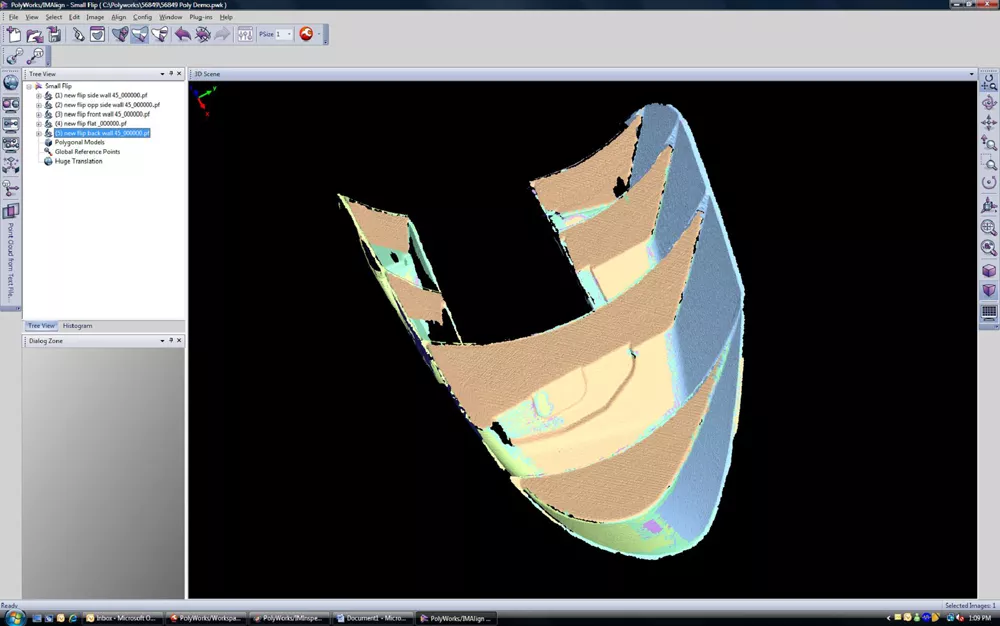
Allineamento delle scansioni e riduzione della sovrapposizione nel modulo IMAlign di PolyWorks
Nell'intero processo, O’Fallon Casting ha usato la digitalizzazione 3D e PolyWorks per ispezionare il modello in schiuma e il getto corrispondente in alluminio. «Importiamo i dati dimensionali nel modulo IMAlign™ del software PolyWorks, dove i percorsi di scansione vengono allineati automaticamente per mezzo di un algoritmo best-fit, andando a creare un modello del particolare basato su una nuvola di punti», spiega Galmiche. «A questo punto, studiamo attentamente il modello per stabilire se disponiamo di tutti i dati necessari a realizzare un confronto accurato con il modello CAD del cliente. Se necessario, piazziamo nuovamente il particolare sulla CMM e acquisiamo i dati dimensionali da un'altra angolazione», aggiunge.
Quando vengono raccolti i dati dimensionali di uno di questi prototipi, O’Fallon Casting opera a una velocità di scansione molto bassa per fare in modo che venga acquisito un elevato livello di dettagli delle entità da ispezionare. Durante il processo vengono raccolti dati in eccesso. «Usiamo la funzione di riduzione della sovrapposizione di IMAlign per eliminare automaticamente l'eccesso nelle aree di sovrapposizione della scansione, quindi creiamo un singolo set di punti di dati che definisce precisamente le dimensioni del particolare in queste aree», spiega.
Successivamente, le scansioni allineate vengono combinate utilizzando il modulo IMMerge™ di PolyWorks per creare un modello di mesh poligonale finemente dettagliato dei particolari digitalizzati.
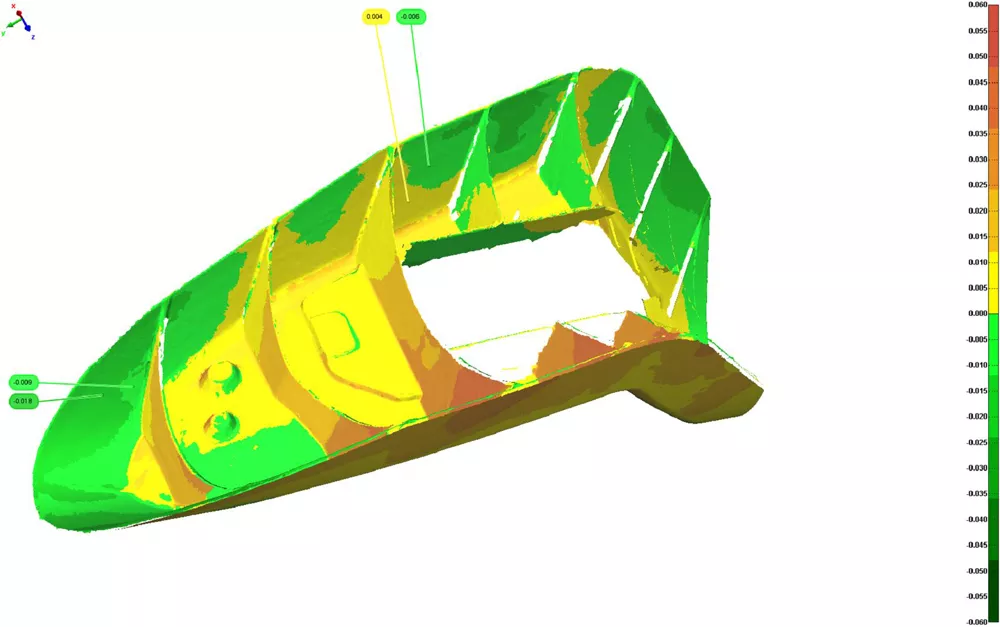
Analisi degli scostamenti globali usando mappe a colori.
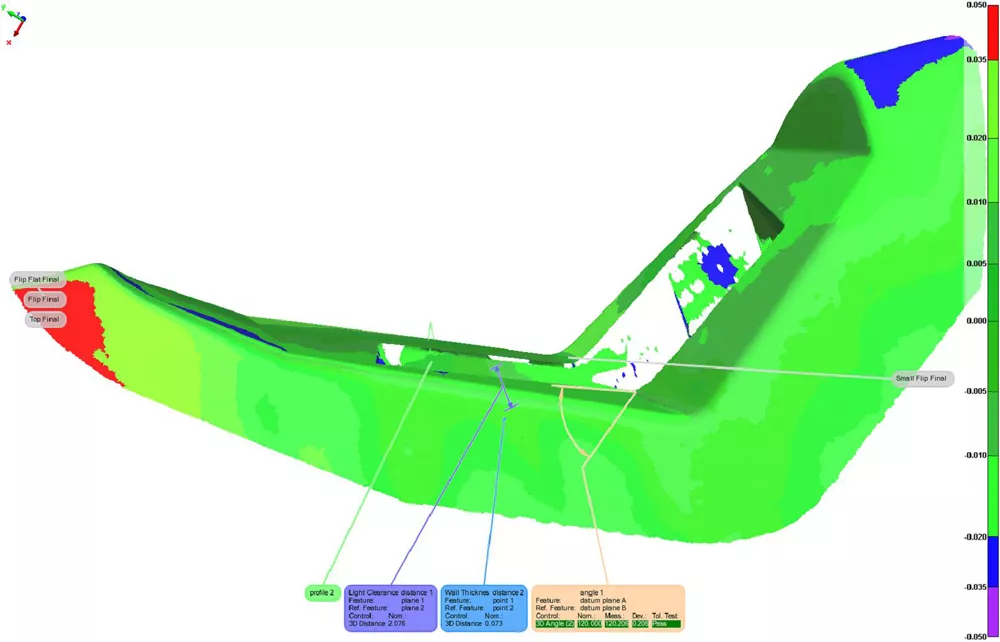
Vengono eseguite analisi dello spessore della parete, del gioco, dell'angolo 3D e della planarità usando il modulo IMInspect di PolyWorks.
«Grazie ai semplici strumenti di IMInspect, siamo in grado di vedere rapidamente in quali punti il particolare è fuori tolleranza rispetto al modello CAD fornito dal cliente», spiega Ben Galmiche, ingegnere addetto alla qualità presso O’Fallon Casting.
Il modello di mesh poligonale è stato quindi esportato nel modulo IMInspect™ di PolyWorks per passare al processo di ispezione dimensionale vero e proprio. Questo pacchetto fa uso di un potente metodo di allineamento dati a CAD, che include il best-fit vincolato e altri metodi basati sulle entità geometriche e sui punti di riferimento. Sono inclusi gli strumenti di confronto e misurazione per ottenere un'analisi completa della superficie e degli scostamenti della sezione trasversale, delle dimensioni delle entità e dei controlli GD&T, del gioco e dello spessore. Per questo progetto specifico, O’Fallon Casting ha utilizzato cinque strumenti specifici di IMInspect per validare l'alloggiamento della luce all'estremità dell’ala:
- È stato eseguito un confronto globale effettuando il calcolo della deviazione tra ciascuno dei punti digitalizzati e il riferimento CAD corrispondente. È stata visualizzata una mappa a colori tenendo conto delle tolleranze fissate da O’Fallon Casting.
- Per fare in modo che il raggio luminoso venga proiettato senza interferenze, è stato misurato il gioco del particolare mettendo a confronto le distanze 3D tra due piani.
- È stato estratto lo spessore della parete calcolando le distanze 3D tra due punti. Questo ne assicura la robustezza e convalida il particolare rispetto ai requisiti di progettazione.
- Sono stati calcolati la planarità e l’angolo 3D tra due piani (utilizzando come riferimenti il datum A ed il datum B) usando il motore GD&T di PolyWorks. È stato prodotto un risultato pass/fail sulla base delle tolleranze prefissate.
Servendosi della funzione di creazione report del software PolyWorks, Galmiche ha preparato un report dell'ispezione usando il formato AS9102. «Oltre ai dati inseriamo alcune istantanee del confronto tra i modelli, per fare in modo che i clienti possano osservare rapidamente i punti in cui il particolare è fuori tolleranza. Siamo anche in grado di mostrare i punti in cui il particolare è solo leggermente o di molto fuori tolleranza, usando colori diversi per rappresentare i vari limiti. Infine, grazie al software di visualizzazione gratuito PolyWorks|Viewer™, i nostri clienti possono vedere i propri progetti di ispezione in 3D direttamente dalle rispettive workstation».
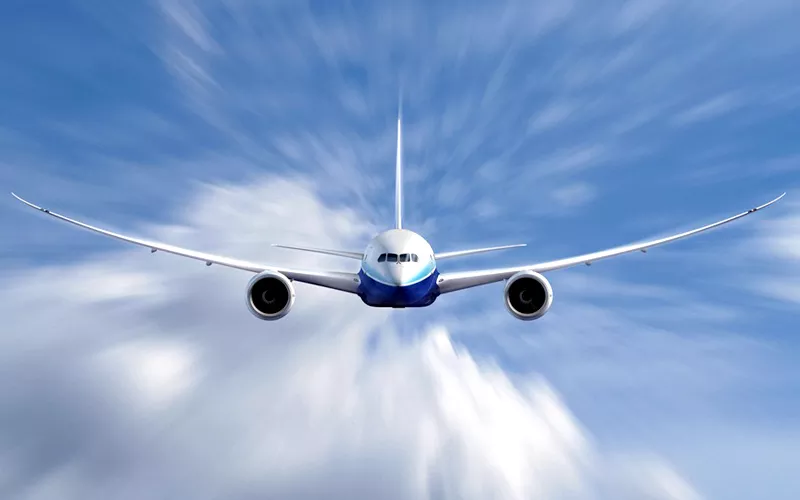
©Boeing
Vantaggi
La combinazione della CMM Global, dello scanner laser Metris XC50 ed il software PolyWorks ha ridotto in modo significativo i tempi di elaborazione necessari alla creazione del prototipo rapido di un particolare presso O’Fallon Casting. «A livello globale siamo molto soddisfatti del nuovo processo di ispezione basato su nuvole di punti», spiega Galmiche. «Per un particolare normale siamo in grado di acquisire i dati dimensionali di cui abbiamo bisogno in circa un giorno, e possiamo eseguire l'analisi dei dati usando il software PolyWorks in meno di mezza giornata. Questo si traduce in una diminuzione di circa il 50% delle tempistiche di processo rispetto al passato. Inoltre la visualizzazione dei dati velocizza il processo di analisi del report dell'ispezione da parte dei clienti, e consente loro di capire meglio le implicazioni derivanti dall’analisi dimensionale dei dati.
Extra
O’Fallon Casting si serve della combinazione CMM/scanner laser/software PolyWorks anche per ispezionare i propri stampi e le proprie attrezzature di raddrizzamento mediante compressione, per garantirne la conformità al progetto. PolyWorks|Inspector mostra rapidamente e precisamente in quali punti l’attrezzatura potrebbe essere logorata o leggermente fuori tolleranza.
Galmiche vede anche un'altra potenziale applicazione di questa nuova suite di ispezione: «Alcuni clienti ci chiedevano di ispezionare componenti particolari all'interno di un sistema per aiutarli a stabilire se le condizioni ambientali, ad esempio il calore, stavano provocando malfunzionamenti. Siamo in grado di realizzare questa operazione velocemente, effettuando una scansione del particolare e confrontando i dati dimensionali reali con quelli del progetto servendoci del software PolyWorks. Questo potrebbe essere un nuovo settore di attività per noi».