À la recherche d'un ajustement parfait
Daimler AG compte sur InnovMetric et Leica pour obtenir un ajustement de pièces parfait.
La gamme de produits de Daimler AG comprend des coupés, des berlines et des familiales haute performance, des minivoitures, des fourgonnettes polyvalentes et des véhicules commerciaux. La deuxième usine en importance de Daimler AG en Allemagne est l’usine de Brême, qui emploie près de 14 000 personnes et a une surface utile de 850 000 mètres carrés. On y produit les cabriolets SL et SLK, de même que toutes les versions de classe C (berline, familiale, coupé et décapotable).
On ne croise pratiquement personne en sillonnant les couloirs en apparence interminables de l’usine ultramoderne de Daimler à Brême. Des centaines de robots travaillent avec une précision chirurgicale : ils mettent en place les différentes pièces en tôle, les soudent, déplacent les pièces terminées vers la prochaine station et transportent les produits finis en hauteur afin de maximiser l’utilisation de l’espace. De loin, ces robots omniprésents semblent danser. Les quelques travailleurs que l’on croise utilisent des bicyclettes on ne peut plus ordinaires pour se déplacer entre les différents secteurs de l’usine : anciennes et nouvelles technologies coexistent en harmonie.
Les progrès technologiques en matière de procédés de fabrication ont permis aux formes plus audacieuses de passer de la table à dessin à la chaîne de montage. Il n’y a pas si longtemps, les véhicules avaient des formes carrées et simples, et étaient composés de pièces assemblées les unes aux autres par des lignes relativement droites. De nos jours, les véhicules ont des formes beaucoup plus complexes. Par le fait même, l’inspection de la manière dont les pièces s’emboîtent les unes dans les autres est une tâche de plus en plus compliquée.
C’est à la division du déploiement des carrosseries brutes et de l’optimisation des procédés que revient cette importante tâche d’inspecter l’assemblage des différentes pièces. Plus important encore, les mesures obtenues servent ensuite à communiquer de la rétroaction aux installations de production afin que ces dernières puissent apporter des ajustements précis et ciblés aux outils.
Dirk Noffke, technicien de métrologie chez Daimler AG à Brême, vérifie l’exactitude dimensionnelle de l’aile gauche de la carrosserie brute d’une Mercedes SLK. La comparaison entre les données réelles et les données CAO se fait en temps réel grâce au logiciel PolyWorks|Inspector.
Le défi
Henning Siemers, ingénieur de l’exploitation, fait partie de cette division responsable des tâches de mesure et d’inspection. Il explique : « Notre rôle consiste à assurer l’exactitude dimensionnelle de la totalité de la carrosserie brute. Une carrosserie comprend une grande quantité de pièces distinctes qui doivent pouvoir être assemblées parfaitement. Notre premier devoir consiste à inspecter la carrosserie brute en entier, c’est-à-dire chacune des pièces et le véhicule dans son ensemble, y compris les écarts entre les panneaux, ainsi qu’à analyser les données recueillies. Selon les résultats obtenus, nous retournons dans les usines de production pour apporter des ajustements aux outils et nous assurer que les pièces du véhicule qui en sortira seront parfaitement assemblées. »
La complexité des formes des véhicules actuels et les tolérances toujours plus sévères ont poussé les instruments de mesure à commande manuelle au-delà de leurs limites.
Par le passé, la division de M. Siemers comptait sur des instruments de mesure à commande manuelle; toutefois, la complexité des formes des véhicules actuels et les tolérances toujours plus sévères ont poussé ces instruments au-delà de leurs limites. « Si l’on observe les véhicules d’autrefois, on constate qu’ils étaient fabriqués à partir de pièces presque carrées qui s’assemblaient assez facilement. De nos jours, les véhicules ont plus de courbes, dont des zones courbes qui changent soudainement de forme et rencontrent d’autres panneaux à différents angles. De plus, puisque les normes de plus en plus élevées exigent un ajustement presque parfait des panneaux individuels, il faut travailler avec des tolérances très sévères. »
La solution
« Avec les formes de plus en plus complexes de nos véhicules, nous avons dû nous mettre à la recherche de nouvelles technologies à la hauteur de nos exigences », a poursuivi M. Siemers. « Il y a deux ans, Karl Heinz Boecker, notre ingénieur du contrôle de la qualité, a découvert au salon CONTROL de Sinsheim, en Allemagne, le système T-Scan de Leica, qui n’était alors qu’un prototype. D’après les spécifications annoncées, nous savions que le numériseur T-Scan de Leica pourrait être la solution recherchée, mais nous voulions avoir la garantie que le produit était bel et bien prêt à être commercialisé. Le principal problème avec les autres solutions de numérisation que nous avions étudiées était que le logiciel n’était pas à la hauteur des appareils. En effet, la collecte de points est relativement simple, mais que faire des données recueillies? Nous avions l’impression que de nombreux fournisseurs prêtaient plus d’attention aux appareils qu’aux logiciels. » Il y a quelques mois, l’équipe de M. Boecker a organisé une démonstration en usine de produits de Leica Geosystems. L’équipement choisi consistait en un laser de poursuite LTD840 jumelé à un palpeur T-Probe et à un numériseur T-Scan de Leica, une combinaison haut de gamme. Le système Leica s’est avéré à la hauteur des attentes.
Le logiciel PolyWorks|Inspector affiche les écarts avec les données CAO à l’aide d’une carte de couleurs ou de vecteurs. L’information est ensuite analysée pour en déduire des mesures correctives, qui sont ensuite appliquées directement aux outils.
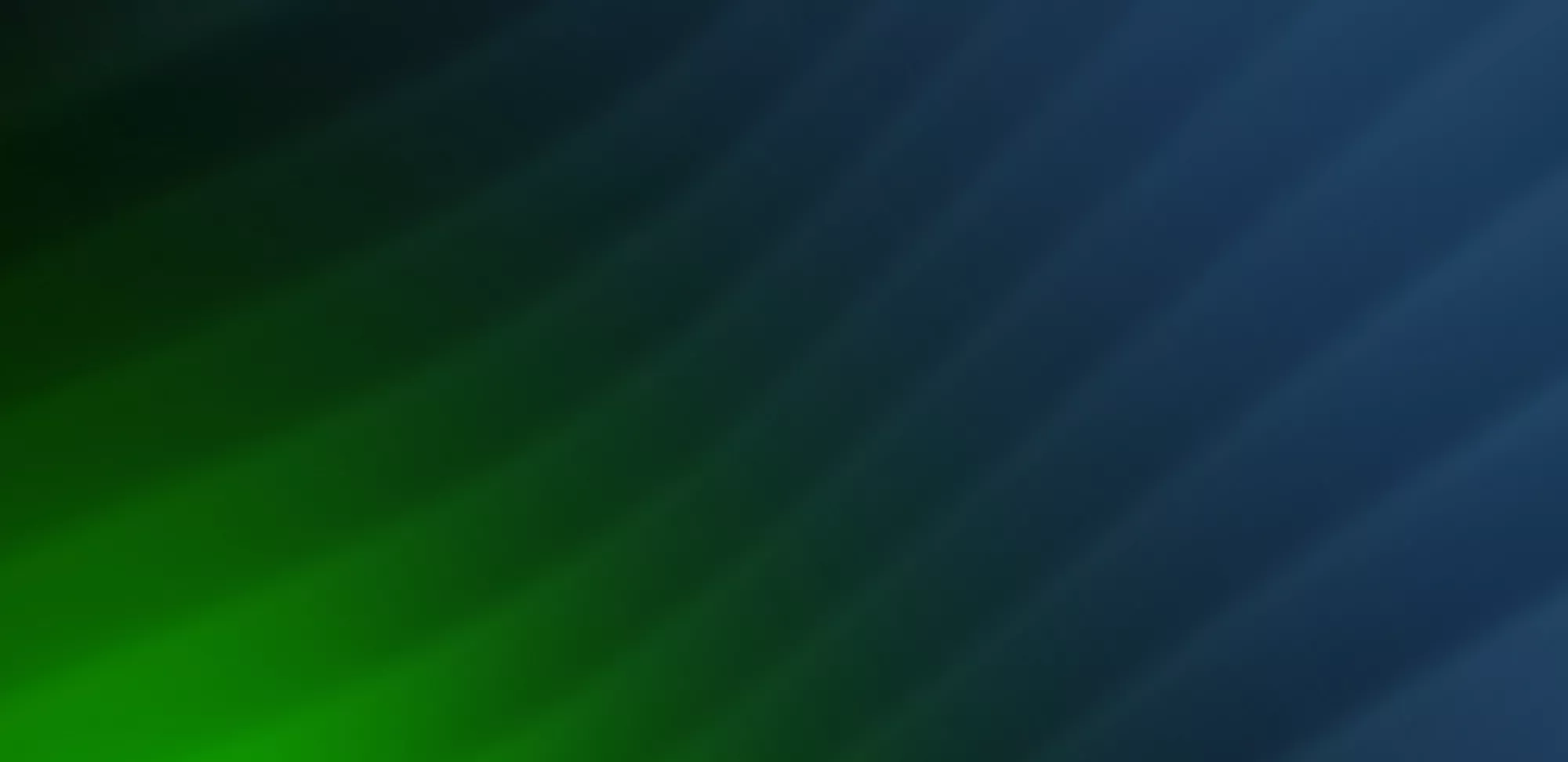
Le numériseur T-Scan de Leica et le logiciel PolyWorks® offraient une combinaison gagnante !
« Nous savions déjà que le numériseur T-Scan de Leica était un outil exceptionnel, et la présentation de la suite logicielle PolyWorks nous a démontré qu’elle était à la hauteur du numériseur. Le logiciel est très puissant, et nous savions que nous étions sur la bonne voie. » Henning Siemers, ingénieur de l’exploitation.
Un vent nouveau
Depuis la livraison du nouveau système, la combinaison T-Probe et T-Scan de Leica a été utilisée, entre autres, pour mesurer les écarts entre les panneaux, examiner les pièces courbes, et inspecter les trous de référence et autres caractéristiques semblables. M. Siemers a également testé intensivement d’autres applications du système T-Scan de Leica : « L’étalonnage à même la chaîne de montage est l’une des nouvelles applications que nous avons découvertes. Auparavant, les carrosseries brutes étaient placées dans un poste grillagé, puis elles étaient inspectées à l’aide d’une machine de mesure tridimensionnelle traditionnelle. Avec 150 palettes et un objectif de mesure de grande précision, on atteint rapidement les limites des méthodes traditionnelles. C’est pourquoi nous voulions prendre les mesures directement sur la chaîne de montage, à la fois des palettes et des outils. Le système T-Scan de Leica a exaucé nos vœux. Dans un avenir proche, nous aimerions également inspecter la ligne de robots en entier. »
Les avantages
Lorsqu’on lui demande ce qui a changé depuis l’implantation du système T-Scan de Leica, M. Siemers répond de manière très précise : « Grâce à la numérisation, je suis en possession d’un plus grand nombre de données utiles. Les analyses partielles sont de meilleure qualité et nous arrivons à trouver beaucoup plus rapidement l’origine d’un problème, ainsi qu’à y apporter des solutions ciblées, par exemple, en intervenant sur les outils à un moment bien précis et en modifiant les paramètres d’après les résultats fournis par PolyWorks. »
Les avantages de l’utilisation du duo T-Probe et T-Scan de Leica et du logiciel PolyWorks sont multiples. « Nous apprécions particulièrement la mobilité du système. L’équipement de Leica Geosystems me permet de recueillir toutes les données dont j’ai besoin en 2 à 3 heures seulement et d’effectuer les analyses plus tard. De cette manière, je ne bloque pas la production trop longtemps, puisque le système nous permet de travailler en parallèle : pendant qu’un opérateur prend les mesures, un autre peut extraire les résultats. »
La combinaison T-Probe et T-Scan de Leica permet de prendre des mesures dans un rayon de 15 m, ce qui laisse aux techniciens un volume de mesure de 30 m. Ainsi, Henning Siemers et son équipe ont l’esprit tranquille : si les exigences en matière de mesure venaient à changer, ils seraient bien équipés pour travailler dans un volume de mesure suffisamment grand pour leur permettre de traiter plusieurs carrosseries brutes simultanément.
Le fait que le système soit modulaire était un élément important pour l’équipe de M. Siemers. « Nous avons acheté un palpeur T-Probe de Leica en même temps que le numériseur T-Scan de Leica. Le mesurage tactile sans fil nous est très utile pour mesurer des pièces qui se tordent facilement, comme le capot. Nous pouvons prendre des mesures rapides avec le palpeur T-Probe de Leica pour avoir une idée générale de l’état de la pièce. Si nous procédions immédiatement à la numérisation, cela nous prendrait plus de temps à réaliser que le capot est tordu. Avec le palpeur T-Probe de Leica, il suffit de recueillir quelques points pour savoir immédiatement ce qu’il en est. Nous effectuons toutes ces étapes dans PolyWorks, en passant simplement du palpeur T-Probe au numériseur T-Scan de Leica, et vice versa. »
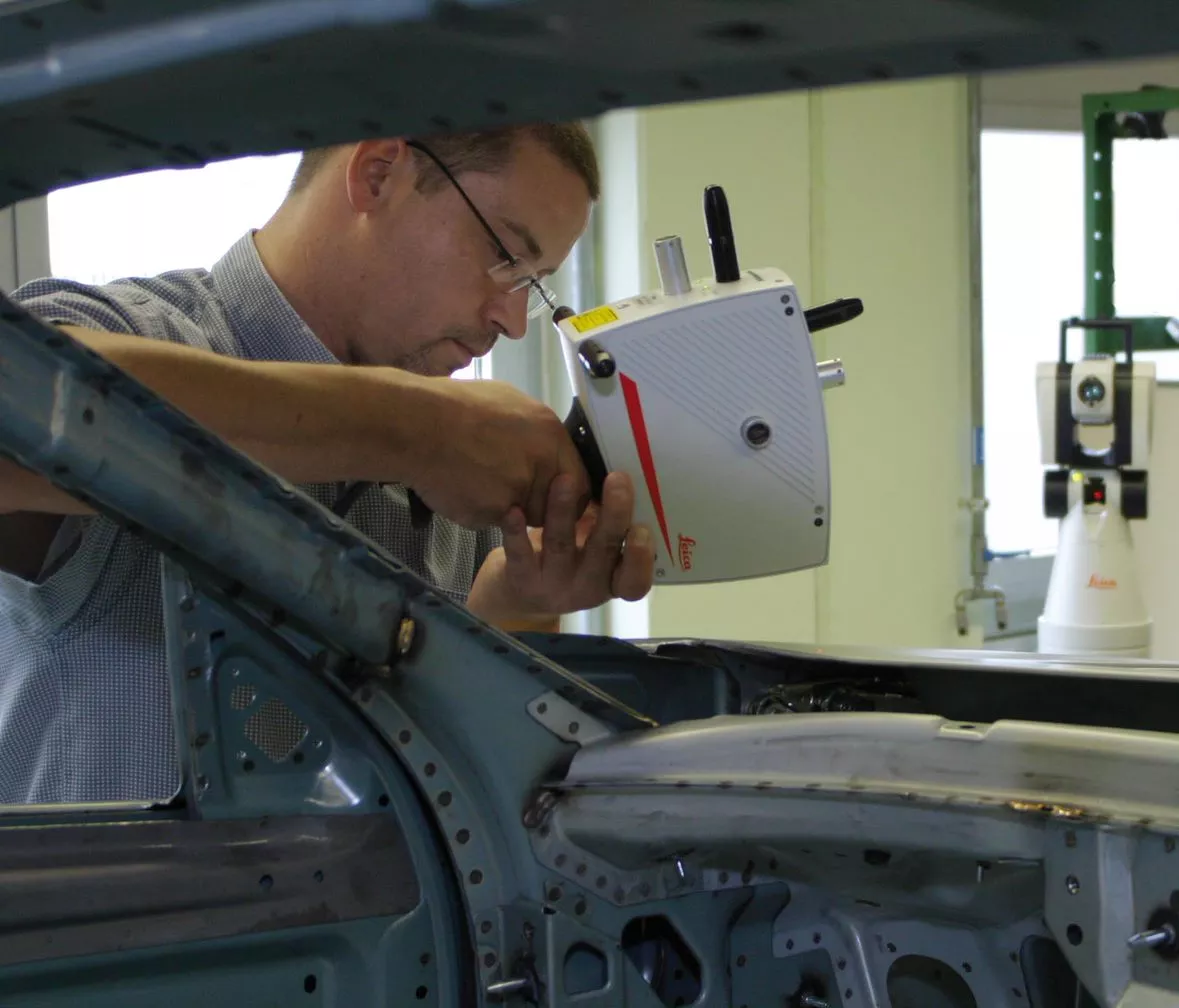
Grâce au vaste volume de fonctionnement du système T-Scan de Leica, qui permet de mesurer un objet dans un rayon de 15 m, il est possible de mesurer un côté de carrosserie brute en entier sans devoir déplacer le laser de poursuite de Leica. L’opérateur se déplace le long du véhicule et le laser de poursuite demeure verrouillé sur le palpeur T-Probe ou le numériseur T-Scan, et ce, partout à l’intérieur du volume de mesure.