Résolution de problèmes de fuites sur des portières de voiture
Grâce à PolyWorks®, Scanning and Inspection Pty a pu analyser la correspondance entre l’encadrement de portière et la carrosserie d’une voiture en moins d’une heure.
Les constructeurs savent lorsque quelque chose cloche. Bien souvent, ce qui s’avère le plus complexe, c’est de trouver l’origine du problème en question. Cette étape exige beaucoup de temps, d’argent et de ressources. Même lorsqu’on réussit à lever le voile sur la source du problème, il faut encore apporter des ajustements avant qu’il ne soit entièrement corrigé. Lorsque la pièce fabriquée diffère du modèle de conception, ou de ce qu’elle devrait être ou a été par le passé, il importe de savoir lesquelles de ses parties sont différentes, et dans quelle mesure. Dans le cas présent, un grand constructeur automobile australien voulait absolument déterminer la source de fuites sur des portières de voiture.
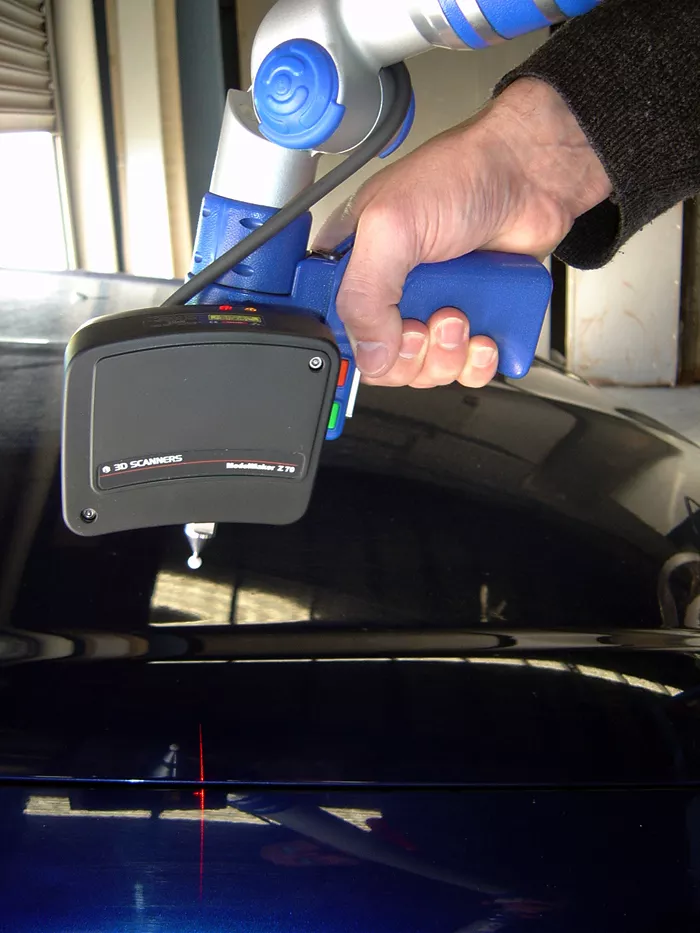
ModelMaker Z70 monté sur un bras FaroArm
Le défi
Un constructeur automobile a récemment vécu l’un de ces scénarios inévitables au cours de l’étape de la fabrication. Il a constaté des écarts dans le recalage de certains joints d’étanchéité de portières côté passager en cours de production et d’assemblage. Il était évident que les voitures construites pendant une période précise de la production étaient conformes aux attentes, et que les portières et les joints étaient tous parfaitement alignés avec le reste de la carrosserie. À l’étape des essais, le constructeur a toutefois constaté des fuites d’eau sur des voitures construites à une période ultérieure. La première tâche consistait à localiser la fuite. Puis, il a fallu analyser la correspondance entre l’encadrement de portière et la carrosserie, ce qui s’est avéré être la tâche la plus complexe. Laquelle de ces deux pièces était différente de celle des véhicules sans fuites? Quelles parties de la pièce étaient différentes, et dans quelle mesure?
Si les véhicules d’un lot n’avaient aucun problème de fuites, mais que d’autres véhicules produits plus tard en avaient, alors il devait bien y avoir une différence structurelle entre les véhicules des deux lots. Dans quelle mesure l’encadrement de portière défectueux était-il différent de celui en bon état? Afin de déterminer les modifications à apporter pendant la production, le constructeur devait être en mesure de quantifier les différences. Le lien et les écarts entre l’encadrement de portière en bon état et celui défectueux devaient être évalués. Une analyse comparative détaillée a été effectuée et, grâce aux récentes technologies de numérisation laser et à la suite logicielle PolyWorks, l’analyse a pu être réalisée en quelques heures seulement.
La solution
L’acquisition de données
Pour recueillir rapidement et efficacement des données de surface, les experts chez Scanning and Inspection ont utilisé un numériseur laser monté sur un bras articulé. Pour ce faire, ils ont utilisé un ModelMaker Z70, soit un numériseur laser de haute qualité capable de numériser une surface à une densité remarquable de 0,05 mm x 0,05 mm, ce qui équivaut à environ 400 points par millimètre carré. Une telle densité permet de créer une reproduction numérique 3D intégrale et réaliste de la pièce, offrant une foule de données n’attendant qu’à être transformées en information utile. Le numériseur obtient sa référence 3D à partir d’une MMT portable, dans le cas présent un bras Platinum FaroArm, dont les mesures ont une répétabilité de ±0,0051 mm, selon la taille. Le bras FaroArm et le numériseur laser MMZ70 ont été transportés sur place sur un robuste trépied à roulettes; ils ont donc pu être aisément installés près des portières en question. La collecte des données de surface nécessaires n’a pris que quelques minutes par voiture.
Le processus d’inspection de PolyWorks
Une fois les données de numérisation recueillies, l’étape de post-traitement de l’analyse pouvait commencer. À l’aide de PolyWorks, des experts chez Scanning and Inspection Pty Ltd. ont virtuellement recalé les données numérisées de la voiture avec fuites sur celles de la voiture sans fuites, puis ils ont réalisé des analyses de comparaison et de mesure de pointe. Toutefois, avant d’effectuer les analyses comparatives, il fallait procéder à une série de manipulations de nuages de points dans PolyWorks.
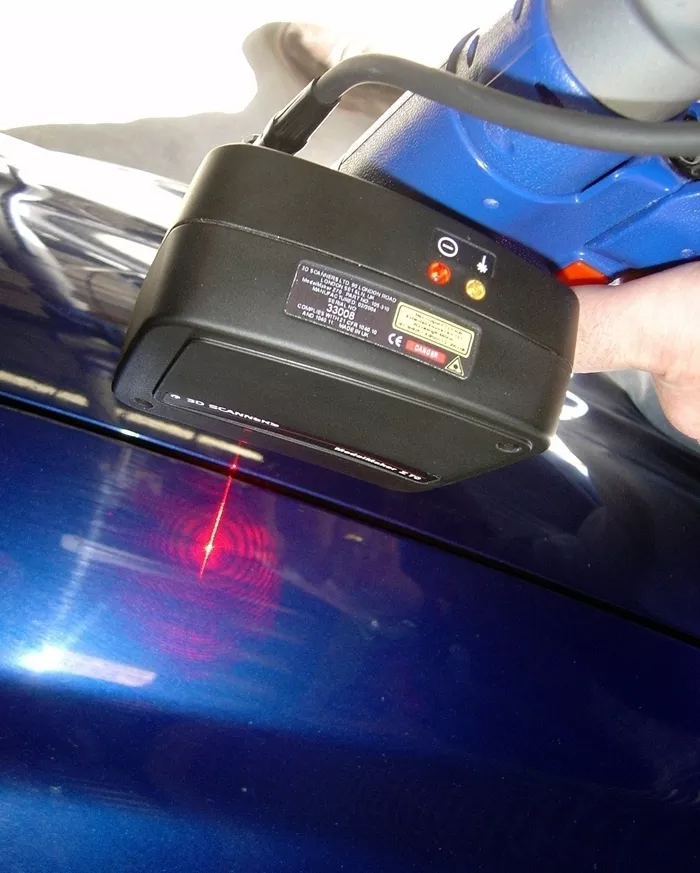
Acquisition de données
Affiner le recalage des numérisations
Pendant l’étape d’acquisition de données, plusieurs passes de scan ont été obtenues. Chaque patch de numérisation est automatiquement recalé à l’aide de la technologie de recalage native du bras articulé qui fournit une référence spatiale pour le changement d’emplacement du numériseur laser. La plupart des nuages de points acquis par le numériseur laser sont superposés aux autres déjà pris en compte par d’autres passes du numériseur. Certaines parties de la pièce sont donc mesurées plus d’une fois. Ces zones de données provenant de plusieurs passes sont appelées « zones de recouvrement ».
Pour affiner le nuage de points recalé obtenu à l’aide de la MMT portable, le module IMAlignMC de PolyWorks utilise ces zones de recouvrement pour recaler toutes les numérisations. D’abord, on a procédé à une analyse des écarts sur le nuage de points recalé. PolyWorks calcule automatiquement les distances moyennes entre chaque numérisation superposée et utilise de la couleur pour représenter une valeur d’écart. D’un simple coup d’œil, les utilisateurs peuvent cibler les numérisations hors tolérances pouvant être améliorées par un nouveau recalage.
Puis, on a procédé à un nouveau recalage à l’aide de la technologie de recalage best-fit de PolyWorks. Pour éviter le glissement entre les patchs avoisinants, huit points de contrôle sont automatiquement réglés pour chaque numérisation, ce qui limite les degrés de liberté. Par cette fonction, PolyWorks se démarque des autres solutions de recalage de numérisations, qui rencontrent souvent des problèmes de glissement pendant le recalage de numérisations. Lorsque le recalage best-fit contraint est terminé, on procède à une nouvelle analyse des écarts, et une carte de couleurs est créée.
La dernière étape consiste à créer un modèle de nuage de points à une seule couche en faisant une moyenne de toutes les numérisations superposées à l’aide de la technologie de réduction du recouvrement de PolyWorks. Le nuage de points obtenu peut ensuite être transformé en une surface qui sera utilisée pour des analyses plus approfondies, comme des comparaisons de portières. La méthodologie de numérisation était la même pour les voitures avec fuites que pour celles sans fuites. La totalité du revêtement périphérique a été retirée des encadrements de vitre et de portière pour n’exposer que les composants de structure en acier post-production. Tout au long du processus de collecte de données, les portières étaient fermées et les zones associées aux joints ayant des fuites ont été numérisées à l’aide du numériseur MMZ70.
Au fur et à mesure que le ruban laser balaie la surface, il collecte des dizaines de milliers de points 3D par seconde, et la surface générée apparaît immédiatement à l’écran. Les capacités de cet affichage de surface de nuages de points en temps réel signifient qu’une zone oubliée, ou toujours en attente de numérisation, pourrait être identifiée au moment de la prise de mesures et prise en compte par la suite.
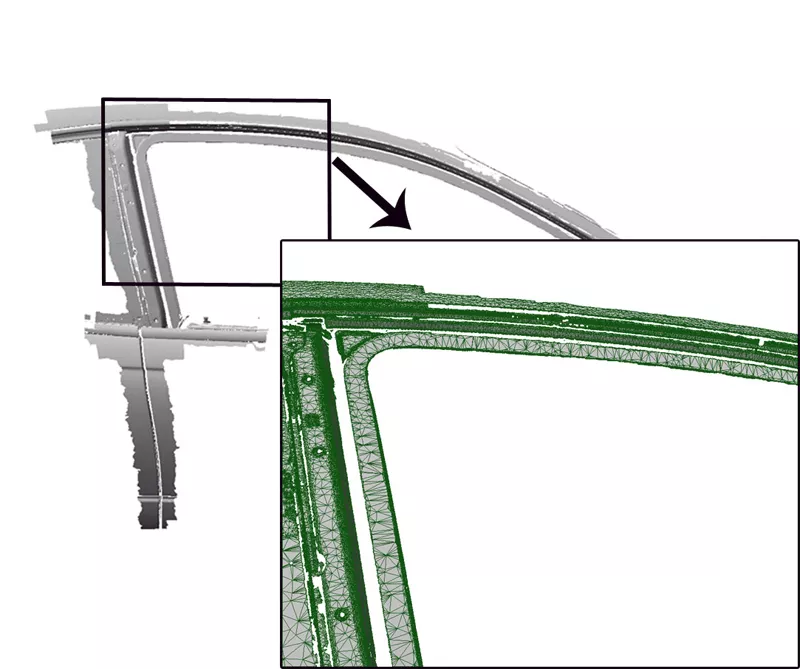
Création d'un modèle polygonal
Créer un modèle polygonal
Pour comparer les surfaces des encadrements de portière en bon état et défectueux, Scanning and Inspection devait convertir les nuages de points en une image pouvant être utilisée comme surface. En une fraction de seconde, PolyWorks a converti des dizaines de millions de points du nuage de points en un maillage triangulaire. Le logiciel a construit des millions de petits triangles en utilisant les points comme des nœuds.
Pour reproduire fidèlement les différentes formes de l’objet numérisé, PolyWorks utilise moins de triangles pour les sections plus constantes de la surface de la voiture et plus de triangles pour les contours plus complexes, le tout en respectant les valeurs de tolérances précisées par l’utilisateur. Les paramètres de distance de recherche et de proximité sont également précisés avant la conversion, et ce, afin de créer la surface triangulaire et de réduire au maximum le bruit inhérent au numériseur.
Les comparaisons de portières
À l’aide d’une série complexe d’analyses de surface et de calculs mathématiques de moindres carrés, les deux ensembles de données numérisées, optimisées et récemment disposées en triangle ont été superposés et recalés grâce à la technologie de recalage best-fit de PolyWorks. Ensuite, PolyWorks a créé un modèle de distribution codée par couleurs en faisant ressortir la comparaison des deux assemblages. La carte d’erreurs de couleurs obtenue permet de repérer facilement les différences entre la portière avec un problème de fuites et celle en bon état.
Les sections inférieures et le pied milieu des portières sont de couleur vert pâle (presque turquoise), ce qui indique un écart inférieur à ±0,5 mm entre les deux portières. D’autres sections, comme l’encadrement de vitre en acier qui est soudé à la portière, sont illustrées en vert, ce qui indique un écart de ±1 à 2 mm. Finalement, la section orange, située sur le châssis de la voiture, indique également un écart de ±1 à 2 mm.
En d’autres mots, lorsque les pieds milieu des deux portières ont été recalés conformément à la tolérance de 0,5 mm, les encadrements de vitre de la voiture avec fuites étaient en fait positionnés entre 0,5 mm et 2 mm plus bas que ceux du véhicule sans fuites, un espace suffisamment grand pour que l’eau s’infiltre.
Les avantages
Les ingénieurs de Scanning and Inspection ont réalisé qu’il serait beaucoup plus facile de changer les soudures problématiques modifiant la position de l’encadrement de portière que d’ajuster le châssis de quelque façon que ce soit. La soudure liant l’encadrement de vitre à la portière a été ajustée pour que l’encadrement ne soit pas si bas (comparativement à la portière sans fuites).
Le processus d’inspection de PolyWorks a été réalisé en entier en moins d’une heure.
Les conclusions tirées de l’examen portaient essentiellement sur les préoccupations du client quant à l’encadrement de vitre de la voiture, ou plus précisément, à la manière dont celui-ci était soudé à la portière. Des ajustements appropriés ont été apportés aux traitements de soudure afin de garantir que les encadrements de vitre ne soient plus assemblés trop loin de leur position idéale, comme illustré par le modèle CAO initial.
La précision et la souplesse du bras FaroArm et du numériseur laser MMZ70, utilisés conjointement avec le logiciel PolyWorks de classe mondiale, ont permis à ce constructeur automobile :
- d’identifier rapidement la source de la fuite;
- de mesurer précisément l’écart physique entre la portière défectueuse et celle en bon état (quelles parties de la pièce étaient différentes, et dans quelle mesure);
- de modifier le processus d’assemblage en modifiant la soudure liant l’encadrement de vitre à la portière;
- de réaliser la totalité du processus d’inspection en moins d’une heure.