Pohyblivé cíle
Software PolyWorks® pomáhá zachovat výkon elektrárny GE
Extreme Fab, Inc. je konstrukční společnost zabývající se kovovýrobou, která disponuje nástroji a dovednostmi ke stavbě masivních strojů požadovaných v odvětví těžby a zpracování ropy a zemního plynu, energetiky, elektráren a nákladních automobilů. Jedním z jejich klíčových zákazníků je společnost GE Aero Energy. GE Aero Energy poskytuje podnikům a komunitám po celém světě možnost kdykoliv generovat spolehlivou a účinnou energii přímo v místě použití nebo v jeho blízkosti, a to v rámci sítě nebo mimo ni.
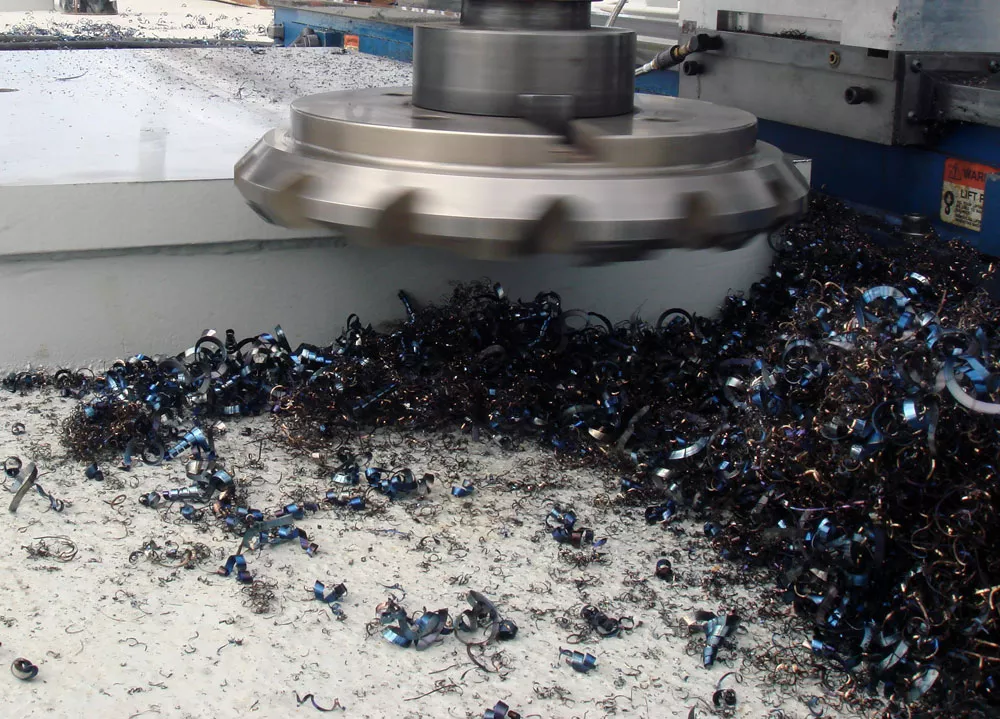
Aeroderivativní plynová turbína FlexAero LMS100 společnosti GE Aero Energy s využitím široké škály pohonných hmot dokáže vygenerovat až 100 megawattů elektřiny při efektivitě konverze 44 %. Tato výjimečná turbína, vytvořená pro rychlé nasazení a instalaci v izolovaných místech, například v odlehlých vesnicích, místech vrtů nebo oblastech náchylných k přírodním katastrofám, je v podstatě elektrárnou „v krabici“. Balíček LMS100 obsahuje turbo plynovou turbínu a kompresor, vše namontované a předem smontované. K zajištění správné funkce tohoto sofistikovaného díla inženýrské práce se používá rozměrný, vysoce přesný rám.
V případě obrábění rámů pro GE Aero Energy spolupracuje společnost Extreme Fab se společností Dimensional Engineering, která poskytuje 3D digitální sběr dat a inženýrské a analytické služby pro řešení výzev v oblasti designu a výrobního inženýrství v celé řadě průmyslových odvětví a aplikací.
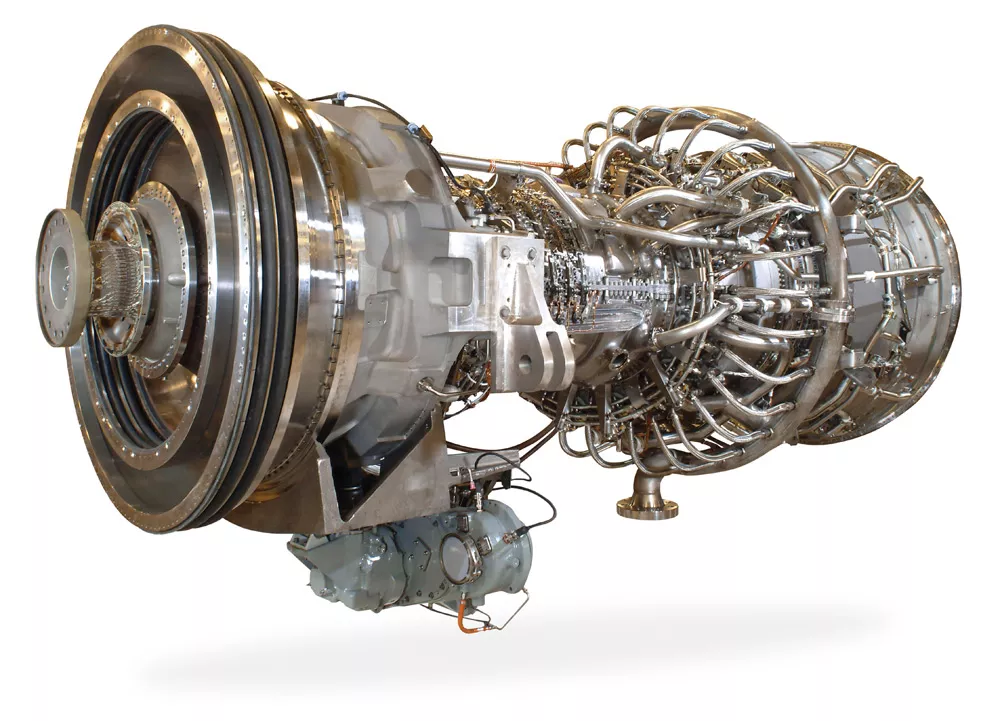
Aeroderivativní plynová turbína LMS100 dodává až 100 megawattů elektřiny.
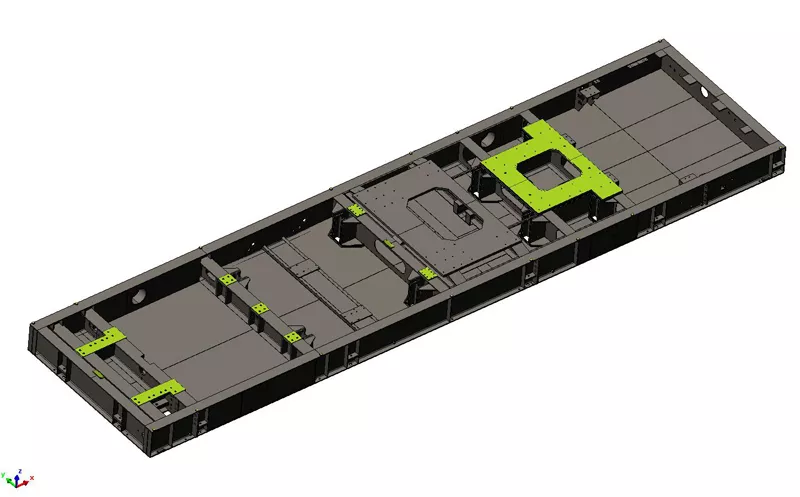
Vykreslení přesně obrobeného rámu 18,3 × 7,6 m. Nosné plochy (zelené) jsou opracovány na rovinnost +/- 0,0508 mm.
„Jenom jednosměrná přeprava rámu stojí tisíce dolarů, takže pokud se musí vrátit do závodu společnosti Extreme Fab k přepracování, jenom další náklady na přepravu se mohou počítat na několik desítek tisíc dolarů,“ vysvětluje Bonner.
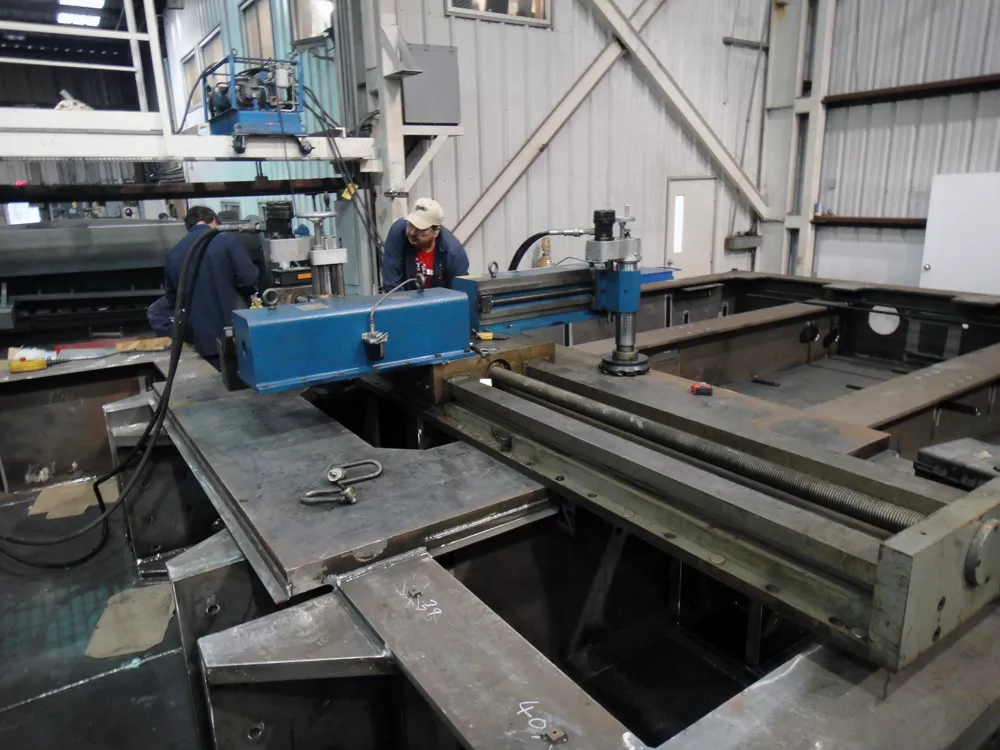
Operátoři provádějí úpravy jednotunového obráběcího systému.
Výzva
Rám pro LMS100 měří 18,3 × 7,6 m a má přesně opracované nosné plochy a montážní otvory. Sebemenší odchylka při obrábění může snížit provozní účinnost, energetický výkon a životnost elektrárny. Podle vyjádření Williama Bonnera, generálního ředitele společnosti Dimensional Engineering „Montážní plochy vyžadují rovinnost +/- 0,0508 mm a vyvýšení +/- 0,127 mm vzhledem ke všem místům po celé délce více než 18metrového rámu.“
Obrobit rozměrný objekt s takovou přesností není samo o sobě snadný úkol a u rámu je to ještě náročnější. „Tato věc se pohybuje, nikdy není statická,“ řekl Bonner. Jednotunové obráběcí systémy „sedí“ na rámu a provádějí přesné řezy. „Pokaždé, když umístíte stroj na rám, ohne se, protože hmotnost stroje není rovnoměrně rozložena.“
Během projektu, který trvá 10 dnů, 12 hodin denně, operátoři stále přemisťují stroj, což způsobuje, že se montážní plochy zvedají, padají, kroutí a přetáčí.
Dalším faktorem, který situaci dále komplikuje, je tepelná roztažnost. Při značných teplotních výkyvech až do 10 °C za 24 hodin se rám celý den roztahuje a smršťuje.
„Role společnosti Dimensional Engineering je řídit nastavení a diktovat úhly a hloubky frézy tak, aby společnost Extreme Fab mohla zajistit přesnost, kterou skupina GE požaduje,“ řekl Bonner.
Pokud hotový rám dorazí do zařízení společnosti GE a nesplňuje požadované specifikace, má to často vážné následky. „Jenom jednosměrná přeprava rámu stojí tisíce dolarů, takže pokud se musí vrátit do závodu společnosti Extreme Fab k přepracování, jenom další náklady na přepravu se mohou počítat na několik desítek tisíc dolarů,“ vysvětluje Bonner. Pokud přepracování ovlivní výrobní plány, neshoda může také znamenat značné finanční sankce.
Throughout the 10-day, 12-hour-a-day project, machinists relocate the equipment , causing the mounting pads to rise, fall, twist, and turn.
Thermal expansion is also a factor that further complicates matters. With considerable temperature variations of up to 50°F (10°C) over a 24-hour period, the skid expands and contracts throughout the day.
“Dimensional Engineering’s role is to control the setup and dictate cutter angles and depths so that Extreme Fab can deliver the precision that GE demands,” said Bonner.
If the skid arrives at GE and it doesn’t meet the required specifications, there are often dire consequences . “It costs thousands of dollars just to ship the skid one way, so if it has to come back to Extreme Fab for reworking, there can be tens of thousands of dollars in additional transportation costs alone,” Bonner explains. If reworking impacts production schedules, non-conformance can also mean significant financial penalties.
Řešení
Při každém pohybu stroje, před každým řezem a po každé operaci, poskytuje společnost Dimensional Engineering společnosti Extreme Fab přesná měření týkající se umístění frézy, polohy frézy a polohy obrobku vzhledem ke statickému, uvolněnému stavu rámu. Bez tohoto měření by bylo obtížné, ne-li nemožné, splnit specifikace požadované společností GE.
Bonner uvedl, že jeho nástrojem jsou laserové trackery FARO a softwarové řešení PolyWorks|Inspector™ od společnosti InnovMetric. „K zachycení přesných měření používáme laserové trackery a k prostudování a správě nasbíraných dat určených k řízení neustále se měnícího projektu používáme software PolyWorks,“ řekl Bonner.
Bonnerův dvoučlenný tým začíná základním zarovnáním rámu v jeho volném stavu. Pomocí 50 referenčních terčů přivařených k obrobku změří laserový tracker základní prvky rámu a software PolyWorks vytvoří globální souřadnicový systém. Software PolyWorks je následně použit k vytvoření několika lokálních souřadnicových systémů, které týmu umožňují izolovat pohyb na samostatných montážních podložkách a zároveň zachovat vztah k celému rámu.
„Pokud bychom nemohli kontrolovat měření s ohledem na přemístění trackeru,
nastaly by velké problémy.“
Po umístění a vyrovnání frézy Bonnerův tým změří rám a polohu frézy, aby poskytl přesná místa, která operátoři využijí k programování hloubky a úhlu řezu. Když je úkon hotový, znovu provedou měření, aby ověřili řez před provedením dalšího průchodu obráběcího nástroje.
Vzhledem k tomu, že se rám při každé změně teploty mění, tým společnosti Dimensional Engineering zpracovává všechna naměřená data pomocí funkcí dynamické kompenzace teploty, které software PolyWorks nabízí. Toto nastavení v kombinaci s přesným umístěním obrobeného prvku umožňuje operátorům stroje naprogramovat dráhy frézy vzhledem k rámu ve stabilních teplotních podmínkách, spíše než podle její aktuální, dynamicky se měnící polohy.
Vzhledem k velikosti rámu a zornému poli jsou laserové trackery FARO během 10denního projektu nesčetně krát přemístěny. To vnáší do přesného obrábění další proměnnou. Aby bylo zajištěno, že veškerá měření jsou přesná vzhledem ke všem polohám trackeru, Bonnerův tým využívá v softwaru PolyWorks funkci pro přesun zařízení a dynamické ustavení v reálném čase. Bonner říká: „Pokud bychom nemohli kontrolovat měření s ohledem na přemístění trackeru, nastaly by velké problémy.“
Aby mohl být projekt dokončen, je provedena závěrečná kontrola, která potvrdí, že rám splňuje specifikace společnosti GE. „Každé měření ověřujeme a certifikujeme, během projektu i před expedicí,“ uzavírá Bonner.
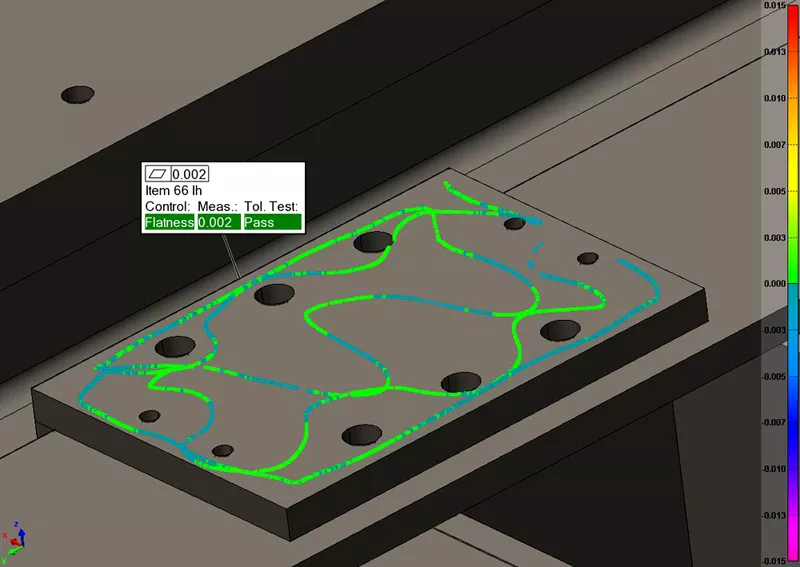
Konečné výsledky kontroly potvrzují rovinnost montážního povrchu.
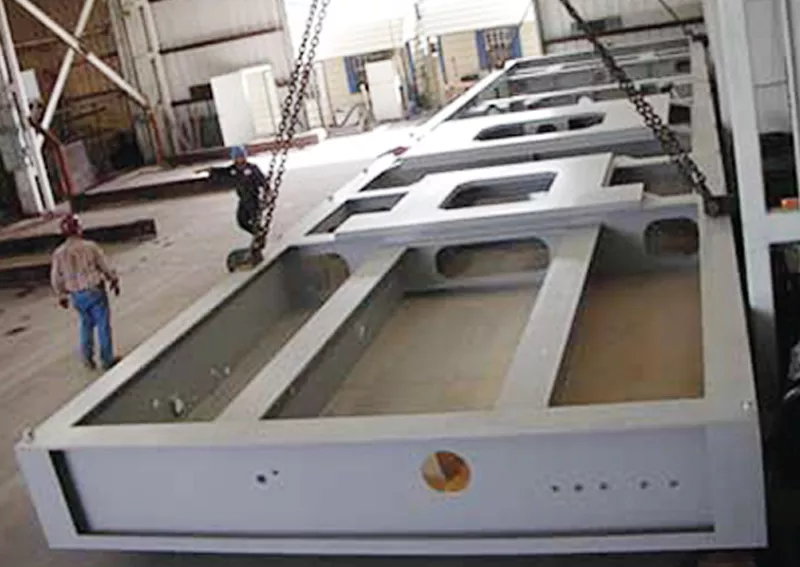
Hotový rám se připravuje k přepravě do společnosti GE.
Výhody
„Bez použití laserového trackeru a řešení PolyWorks|Inspector by nebylo možné dosáhnout této úrovně přesnosti a preciznosti, alespoň ne kvantifikovatelným způsobem,“ řekl Bonner. „Tuto práci děláme již šest let a dosud jsme dělali na více než 50 rámech. A ani jeden z nich nemusel absolvovat tu drahou zpáteční cestu kvůli přepracování.“ Za celých šest let dostala společnost Dimensional Engineering pouze dvě zprávy o neshodě (NCR): první se týkala jednoho otvoru, který nevyhovoval specifikacím, a druhá byla způsobena protichůdnými specifikacemi ve výkresech rámu.
Společnost Dimensional Engineering používá stejný proces a nástroje i pro další rozsáhlé projekty, včetně pomocných komponent pro balíček LMS100, jako je mezichladič. „Techniky použité u měření rámu se používají k umístění dvou 15metrových montážních kolejnic chladiče během jejich svařování, 120 otvorů na montážní přírubě chladiče a rovnoběžnosti na vstupních a výstupních přírubách,“ vysvětluje Bonner. „Bez přesných měření, která získáváme pomocí laserového trackeru FARO a softwaru PolyWorks, by chladič nepasoval do mezichladiče a mezichladič by nepasoval správně s turbínou LMS100.“
Díky softwaru PolyWorks jsou tedy pohyblivé cíle pro společnost Dimensional Engineering říditelné a obrábění rozměrných dílů je předvídatelné.